Strengthening the Core of Manufacturing in PA
The University of Pittsburgh received more than $550k in grants through the Pennsylvania Department of Community and Economic Development’s Manufacturing PA Innovation Program
Since the Second Industrial Revolution, Pennsylvania has been at the forefront of developing new energy technologies, from oil and gas to nuclear and renewables. Thanks to new funding from the Commonwealth, faculty and their students at the University of Pittsburgh Swanson School of Engineering received more than $558,749 in grants for projects that will move the Pennsylvania economy forward.
The Pennsylvania Department of Community and Economic Development’s Manufacturing PA Innovation Program awards projects that utilize engineering and science to keep Pennsylvania a national and international leader in manufacturing, as well as achieve the full economic potential for high-paying manufacturing jobs.
The projects funded were recently announced by Secretary Rick Siger at the sixth annual Manufacturing PA Innovation Program Expo, held recently in Harrisburg.
"Partnerships between academia and industry can have remarkable outcomes, but being able to also support undergraduate and graduate students in research can challenge young minds and help to secure the future of innovation and the workforce needs in Pennsylvania,”" said David Vorp, Senior Associate Dean for Research & Facilities and John A. Swanson Professor of Bioengineering at Pitt.
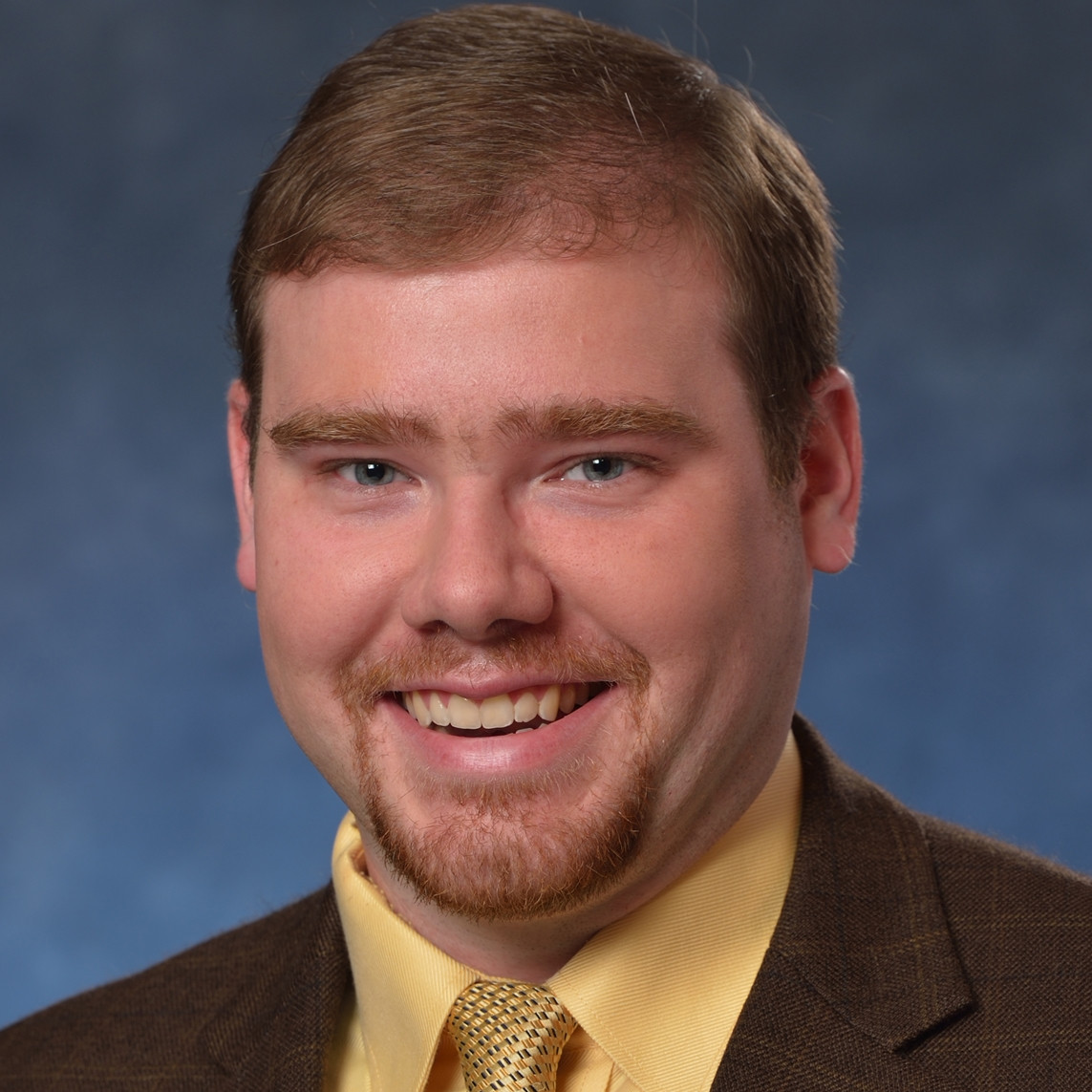
Brandon Grainger, Associate Professor of electrical and computer engineering and Eaton Faculty Fellow
Grainger received $69,999 for his project, “Power Electronics Based Measurement System for Characterizing Magnetic Components.”
This project will design a measurement testbed for magnetic components to accommodate magnetic manufacturers and for training multidisciplinary electrical engineers. Magnetic components are critical to renewable energy systems and electric vehicles, and engineers prefer to consult component datasheets that list various design parameters. However, datasheet tied to component characterization and loss are limited in value. By creating a higher voltage testbed, Grainger’s team will be able to close this gap and ensure electrical systems operate at peak efficiency.
Grainger’s team will use CorePower Magnetics’ magnetic components in Pittsburgh to test their designed testbed.
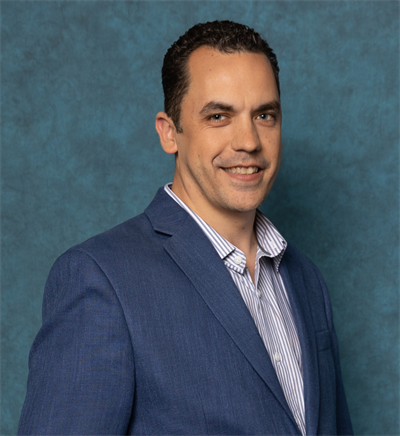
Paul Ohodnicki, Associate Professor of Mechanical Engineering and Materials Science
Ohodnicki received $70,000 for his project, “In-line laser-based advanced manufacturing of nanocrystalline allows for electrification applications.”
Traditional batch processing suffers from lack of scalability and quality control challenges and limits potential for rapid thermal processing to optimize magnetic and mechanical properties.
Through this project, Ohodnicki and his team are looking to establish laser processing as a viable method for scalable, continuous processing of nanocrystalline soft magnetic alloys and to replace batch processing. The end goal is to develop a laser production process capable of producing magnetic cores with improved mechanical and magnetic properties with high throughput.
Ohodnicki’s team will integrate this new technology into CorePower Magnetics products in Pittsburgh.
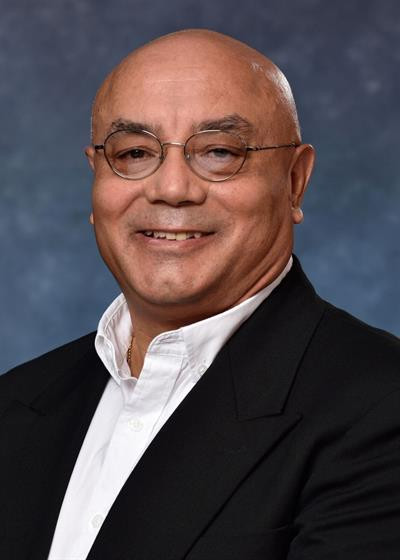
C. Isaac Garcia, Research Professor of Mechanical Engineering and Materials Science
Garcia received $70,000 for his project, “Cost Effective Alumina Forming in Cast Stainless Steels Alloys for High Temperature Allocations.”
The project focuses on high temperature oxidation behavior of a new type of alumina-forming alloys used in high temperature applications. The new alloy would replace the currently used TMA6350 alloy in the manufacturing of components like furnace rolls, radiant burner tubes, and ethylene tubes for the steel and petrochemical industries. The anticipated alloy will be devoid of Hafnium and minimize the use of rare-earth elements, expecting to reduce production and component costs by 30-35 percent.
Garcia’s team will partner with Duraloy Technologies Inc. in Scottsdale, Pa. and Cleveland-Cliffs in Coatesville, Pa.
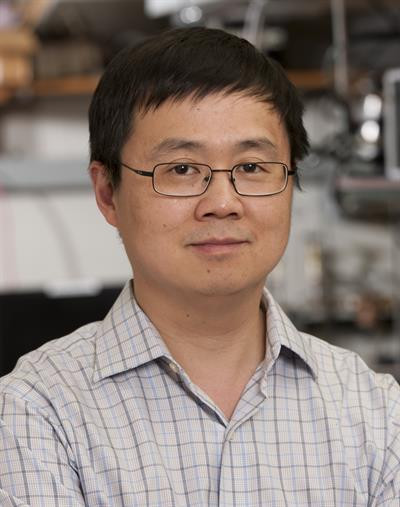
Kevin P. Chen, the Paul E. Logo Professor and Vice Chair for Research of Electrical and Computer Engineering
Chen received $70,000 for “Adaptive Ultraviolet Laser Optics Fabrication of Shark-Fin Coating for Aerospace Applications.
The project will develop a robotic laser fabrication technology to create texture in surface coating to improve aerodynamics and hydrodynamics performance of aircraft and ships. Thiswill enable new laser manufacturing techniques with self-stabilization capabilities to rapidly produce micron-size features using industry robots across the surfaces of aircraft and ships.
Chen’s team will partner with R&D Coatings Inc. in McKees Rocks, Pa., Michael Dvorchak Enterprises LLC in Monroeville, Pa., and Covestro LLC in Pittsburgh.
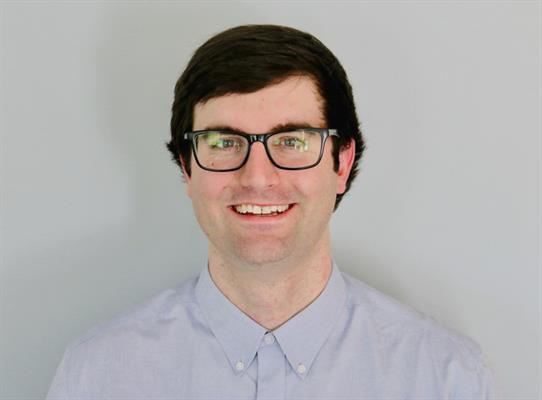
Zachary Harris, Assistant Professor of Mechanical Engineering and Materials Science
Harris received $70,000 for his project, “Creating a Pennsylvania-Centered Supply Chain for Additive Manufacturing of Cu-Ni Components.”
Cupronickel components are widely utilized in seawater-facing infrastructure on marine vessels due to their excellent resistance to corrosion, but supply chain challenges in the casting industry are causing significant delays in new vessel construction. To eliminate these logistical bottlenecks, Harris’ team will develop a Pennsylvania-centered supply chain to produce cupronickel components through metal binder jet printing. Over the course of the project, the research team will first identify best practice approaches for creating acceptable cupronickel parts with metal binder jet printing and then demonstrate that these optimized components can meet current corrosion and mechanical property specifications. Successful demonstration of such properties will open the door for local western Pennsylvania businesses to become on-time and on-demand suppliers of critical components in support of new vessel construction efforts.
Harris’ team will partner with Metal Power Works in Clinton, Pa. and ExOne in North Huntingdon, Pa.
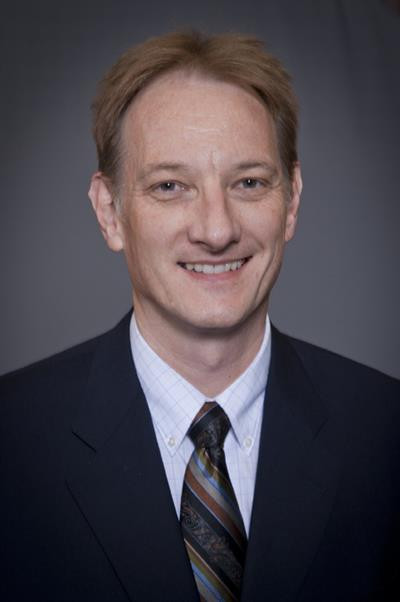
Jörg Wiezorek, Professor of Mechanical Engineering and Materials Science
Wiezorek received $68,750 for his project, “Spheroidal Ti-powder preparation by energy frugal up-converting of machining scrap secondary feedstock.”
Wierzorek’s team will study upconverting titanium (Ti) chip-scraps from machined (subtractive) alloy components into high-value, high-demand Ti stream powders for the powder metallurgy and additive manufacturing sectors, creating a sustainable and energy-efficient supply chain for biomedical and aerospace industries throughout Pennsylvania.
Wiezorek’s team will partner with 6K Additive in Burgettstown, Pa.
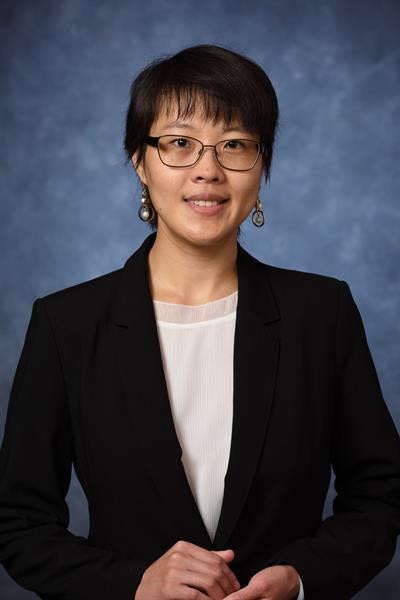
Xiayun Zhao, Assistant Professor of Mechanical Engineering and Materials Science
Zhao received $70,000 for her project, “Enhancing Binder Jetting based Ceramics Additive Manufacturing via In-situ Process Monitoring.”
Ceramic materials present supreme properties for numerous applications. Binder jetting (BJ) is a cost-effective, low-energy additive manufacturing (AM) technology, which builds parts by spreading powder layers and joining powders selectively with jetted binders. BJ based AM (BJ-AM) holds the promise to transform ceramics manufacturing due to its design flexibility, high scalability, and broad material choices. However, current BJ-AM processes still tend to produce green parts with limited density and high porosity. The objective of this project is to develop an in-situ process monitoring technology, which is based on fringe projection profilometry (FPP), for online detection of process abnormalities and print surface defects during ceramics BJ-AM.
Zhao’s team will partner with Du-Co Ceramics Company in Saxonburg, Pa.
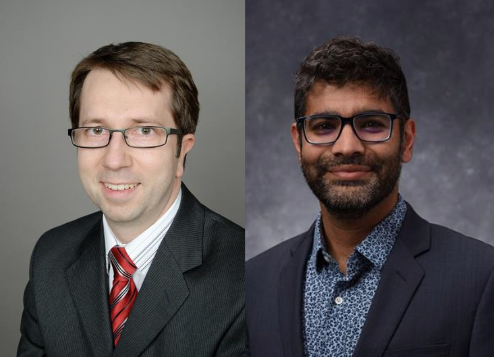
Assisociate Professors of Mechanical Engineering and Materials Science Nikhil Bajaj and Markus Chmielus
Chmielus and Bajaj received $70,000 for their project, “Development of Industry-Relevant Test Equipment for Magnetic Shape-Memory Alloy Actuators.”
The proposed study combines complementary expertise of Aerotech and Professors. Chmielus’ and Bajaj’s groups on the production and testing of functional magnetic shape memory alloys (MSMA), systems modeling and controls, and linear motion and actuation design. Although MSMAs have unique actuation properties (high frequencies of up to 600 Hz, and large strokes of up to 12 percent, and self-limiting capability), applications are still constrained by the lack of industrial expertise. Aerotech, a Pittsburgh-headquartered company with local R&D and manufacturing facilities, requires the ability to test the performance of MSMA elements and actuators in order to pave the path towards widespread, reliable, demonstrable, and performance-standardized MSMA actuators. To achieve this goal, this project aims to design, model, build, and validate industry-relevant testing equipment.
Their team will partner with Aerotech in Pittsburgh.